According to the latest figures from the Health and Safety Executive, 36.8 million working days were lost in the UK, due to work-related illness and workplace accidents in 2020/21. Businesses are continuously looking for ways to avoid injury at work and improve wellbeing and workplace safety because the benefits are clear – a healthy, engaged workforce and improved productivity.
The introduction of Artificial Intelligence is currently transforming workplace safety and productivity in the UK following the US lead where the fast growth of the AI wearable device market for health and safety monitoring means the market is more mature.
In the UK, wearable solutions are now becoming more popular, with new AI health and safety monitoring devices like the Modjoul SmartBelt and WearHealth exoskeleton suit analysis bringing exciting and disruptive change. Wearable devices bring with them a new way of harnessing detailed data that can help inform future workplace health and safety policy within organisations.
These technologies often work together as part of a holistic solution with each technology forming part of a dynamic ecosystem. Each one plays its role in keeping the worker safe and reducing workplace accidents. Let’s take a closer look at some of the technologies included in the new wearable devices currently on offer:
– AI solutions for musculoskeletal disorders
Wearable tech to report ergonomic activities in the workplace is on the increase with exoskeleton suits increasingly being used in the UK workplace to help keep workers safe when carrying out high impact repetitive activities. Granular reporting on bends, twists, stooping, crouching, reaching and carrying, can be processed in great detail to offer insights of a global workforce risk analysis.
Technology providers like WearHealth match the right exoskeleton suit to the activity being performed with the aim of ensuring their usual daily tasks can be performed without the risk of injury or suffering from musculoskeletal disorders. Video scanning technology is used to assess a particular task, make recommendations for possible exoskeleton suits and then report on this with sensor analysis of the activity. The sensors are worn by the worker to allow for analysis of an appropriate exosuit, and determine comfort and support based on real time data generated during the task. The right exoskeleton for that task can then be fitted and used as required based on the potential effectiveness and useability.
In occupations where repetitive injury strain, motion sensors can help to monitor tasks. For example, Ansell, the world’s largest supplier of PPE, has launched a new technology called InteliforzTM which monitors repetitive hand and wrist movement to protect against a range of hand and wrist injuries including carpal tunnel syndrome. A motion sensor pod worn in the safety glove alerts the user when carrying out a risky hand movement by using a haptic buzz. This also reports potential issues to management which allows the correct intervention to reduce risks.
– Wearable technology using Radio Frequency Identification (RFID)
In the Health and Safety field, an RFID tag can be used to ensure that people are wearing the right PPE for a restricted area. Each piece of PPE – gloves, mask, boots – will contain a tag and if one or some of the tags are missing when a person passes through a sensor, an alarm sounds, alerting the user to the fact that they are not correctly dressed for the area that they are entering. It can also be used to track the location of wearable AI technology. For example, the Modjoul SmartBelt needs to be charged at the end of the day but if the user forgets to remove it, sensor towers stationed near the exit remind them not to leave while wearing it and to replace it in the charging bank for the following day.
– Dynamic provisioning using Bluetooth technology
Bluetooth technology can be used in the workplace to help keep track of equipment and people to ensure that they are kept safe. It is incredibly versatile and can be utilised in a huge variety of situations. For example, if every staff member and visitor is issued with a wearable Bluetooth device, then by simply scanning the code on any device, the platform will detect their profile. This dynamic provisioning technology allows you to track who is in and out of a building in the case of an emergency. A Bluetooth beacon can be used in restricted areas to regulate access to people with the correct authorisation, in a process called Zoning.
– Wideband Technology to prevent collisions
Wideband active technology is installed via transmitters on forklifts and mobile equipment. Colleagues wearing similar technology are informed with the driver, that a collision is possible. Full reporting of near misses and proximity are stored for review. This technology goes a long way towards helping reduce workplace accidents.
– Wi-Fi for monitoring
Technologies which have wireless capabilities like the Modjoul SmartBelt, will detect lack of movement and send an alert or email to that worker’s manager if a worker suddenly stops moving. The Bluetooth beacon will then tell them which zone that person is located in the building, so they can be found if they are unconscious. If the person is conscious when they trip or fall, they can use the same technology to send an SOS or email to the manager by pressing a button on the belt.
Temperature controlled environments can be a feature of food led workplaces and Wi-Fi technology can be used to monitor exposure to extreme temperatures. A wearable device then alerts the user that they have spent too long in that environment and that they need to remove themselves to a more temperate area. It can also monitor light levels and tell the user if they have been working in an environment that is too light or too dark.
– Data analysis to improve training and reduce workplace accidents
One of the key benefits of all these wearable AI technology solutions is the detailed data it collects related to the workplace environment, and the operations carried out. The data provided is in real time which means that the technology is continuously measuring and tracking progress. Analysis of this data can pinpoint issues, provide risk assessment of specific tasks, and be customised to fit specific situations. This data is invaluable in helping the workplace to operate more efficiently and improving workplace wellbeing.
The AI wearable technologies coming on stream in the UK are really exciting, providing real disruption and real change to an area of workplace wellbeing that can really benefit from the advantages that AI provides.
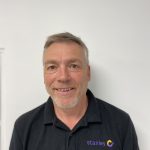
Graham Sharp
Graham Sharp is the Managing Director of Stanley. Graham was introduced to Stanley in 2014. After just six months, Graham was promoted to MD where he remains committed to capitalising on Stanley’s strong heritage and experience to continue to build the business into a world-class leading Health and Safety focused Specialist. By motivating, coaching, and encouraging Stanley’s people Graham leads from the front in striving for excellence on every project undertaken. He also believes that understanding the needs of clients and delivering a high-quality service, will see continued growth for Stanley.